The chemical industry relies on naturally occurring organic carbon sources, primarily derived from fossil fuels, and converts those in a complex production network into valuable products. A portion of these carbon sources is used for meeting the energy demands of the processes involved. Throughout history, the raw material base of the industry has changed from wood over coal to crude oil and natural gas. While renewable carbon sources are also used, their usage remains limited and is specific to certain value chains.
When considering global industrial emissions, the chemical industry ranks as the third-largest industrial emitter of carbon dioxide, following steel and cement production. Consequently, decarbonization strategies are of utmost importance and hold high priority within the industry.
1 Global Raw Material Availability: Germany as a Case Study
Today’s petrochemical industry is predominantly based on naturally occurring (largely fossil) carbon sources—oil, gas, coal, and biomass—and converts those into a plethora of commercial products. The raw material mixes and the share of the primary chemicals differ between the regions.
Whereas in Europe, (imported) oil is the most important carbon source, in North America, ethane from shale gas takes an increasing share. In China, a significant fraction is coal-based, and in Russia, natural gas dominates. On the product side, high-value chemicals (HVCs, olefins, and aromatics) dominate, except in China, where HVCs, ammonia, and methanol have equal shares. The sizes of the circles in Figure 1 reflect the sizes of the respective markets.
Figure 1. Primary feedstock use and chemical production by region [1]. The left pie chart of the pair for each region displays feedstock usage, while the right pie chart displays primary chemical production. The pie charts are sized in proportion to the total quantity (million tonnes of oil-equivalent (Mtoe) or million tonnes (Mt)) in each case.
The carbon base of the chemical industry is closely linked to the energy sector, where the same raw materials are used, although on a much larger scale. Figure 2 shows the German energy flow scheme which is annually published by the “Arbeitsgemeinschaft Energiebilanzen” (Workgroup Energy Balances). Non-energetic uses, essentially the carbon base of the chemical industry, account for just 7.9 % of Germany’s primary energy [2].
Figure 2. Carbon base of Germany’s chemical industry linked to the energy sector [2,3]. Left side: Energy Flow Chart for the Federal Republic of Germany in 2021; Petajoule (PJ). Right side: Raw material base of German chemical industry in 2020.
The current raw material use of the German chemical industry is shown on the right side of Figure 2. Whereas oil and renewables predominantly end up in the produced materials, about 75 % of the gas is used to drive the conversion processes. The two most significant gas-fired processes, steam cracking and syngas production, are crucial stages in the production network. Steam cracking is a refining process that breaks down heavy hydrocarbon molecules into lighter ones, while syngas production involves the conversion of carbon-containing feedstocks into a mixture of hydrogen and carbon monoxide gases. Both processes need high temperature process energy and cannot easily be switched from gas to alternative energy sources. Therefore, local price peaks in the gas supply, as in 2022, are an existential threat to the industry in Germany.
Figure 3. The “Chemis-tree” (term coined by BASF [4]) and an aerial view of BASF’s Ludwigshafen site.
The petrochemical industry operates through an interconnected network of plants, often referred to as “Chemis-tree.” One prominent example of this concept is the Ludwigshafen home site of BASF in Germany (see Fig. 3), which stands as one of the largest in the world. As The Times put it in 1988, “They pump in natural gas, oil, and salt, make many products, and use the byproducts internally. There is only very little real waste.” [5]
2 Historic Changes of the Raw Material Base
2.1 Wood
The precursor of today’s chemical industry, similar to the energy sector, relied on wood as a carbon source. The primary occupation of the charcoal burner was the production of charcoal for metallurgical purposes.
Figure 4. Wood Gasification. Left side: Distribution of products [%] from the gasification process of dry beech wood. Right side: Charcoal kiln [6].
The fumes from the charcoal piles (see Fig. 4) were released into the atmosphere. It was only later that their additional value as a gaseous raw material feedstock was discovered. Thus, a more sophisticated version of char burning was developed, for example, with the so-called Reichert retort, where the waste gases were retained and chemical processes based on those gases were established. For further details see Ref. [7].
2.2 Coal
Following the invention of James Watt’s steam engine, coal instead of wood became the main energy source during the 19th century. The coal was processed and refined in coking plants, where the desired products were metallurgical coke and coke oven gas, primarily used for lighting purposes. During this process, a small fraction of tar is also formed, which was originally considered as a nasty byproduct (see Fig. 5).
However, this tar turned out to become the foundation of today’s chemical industry after the discovery of synthesizing dyes from aromatics in the laboratories of Friedlieb Ferdinand Runge, August Wilhelm von Hofmann, and William Henry Perkin. The high content of aromatic compounds in the tar fraction turned it from waste into a valuable raw material, and at the end of the 19th century, tar was the main raw material of the developing chemical industry. In Germany, the “Teerfarben-Fabriken” Farbwerke von Meister, Lucius, and Brüning (German for “Coal-tar Dye Factories Dye Works of Meister, Lucius, and Brüning”) in Hoechst, the Farbenfabrik Fr. Bayer & Co. in Elberfeld, and BASF (Badische Anilin und Sodafabrik; German for “Baden Aniline and Soda Factory”) in Ludwigshafen were founded. During this first stage of the coal age, the chemical industry again (similar to the wood age) used a byproduct of the energy sector as a raw material.
Figure 5. Coking of bituminous coal. Product yield [%]. [8]
The chemical composition of coal is roughly “CH”; thus, coal has a deficiency in hydrogen. Therefore, in a second stage of the coal age, various upgrading technologies in addition to the original coking process were developed specifically for the chemical industry:
- Coal Gasification: Production of synthesis gas (“syngas”, CO/H2), and syngas-downstream chemistry such as methanol and ammonia synthesis and the Fischer–Tropsch synthesis
- Coal Hydrogenation: Catalytic conversion into liquid hydrocarbons at ca. 100–200 bar hydrogen pressure
- Acetylene synthesis via calcium carbide, and acetylene downstream chemistry, e.g., Reppe chemistry
In 1923, exactly a hundred years ago, BASF started the operation of the first large-scale methanol plant in Leuna [9]. This groundbreaking facility utilized synthesis gas (syngas), thereby revolutionizing the production of methanol on a massive scale and completely replacing the original wood-based production method. The high-pressure process used coal-based synthesis gas and a zinc chromite (Cr2O3-ZnO) catalyst developed by Alwin Mittasch [10]. Later, copper-based catalysts were developed, which today allow the process to be run at much lower pressures compared with the original process layout.
Coal hydrogenation and Fischer–Tropsch technologies were of strategic importance for Germany’s fuel supply during World War II. For similar reasons, large coal-based Fischer–Tropsch plants were built in South Africa during Apartheid. Those plants are still running, although in part switched from coal to natural gas. The last Fischer–Tropsch plant in Germany was operated until 1972 in Schwarzheide (former GDR (German Democratic Republic in German DDR (Deutsche Demokratische Republik)).
2.3 Oil
Usually, the beginning of the oil age is linked to the first successful drilling by Colonel Edward Drake on August 27, 1859, in Titusville, Pennsylvania, USA (see Fig. 6). The fact that the very first oil well was drilled in Northern Germany, close to a small village named Wietze, is less well-known.
Oil-containing sands were known in Wietze since the 17th century. The local farmers extracted the oil from these sands, and sold them as “Luzifer’s bacon”. The product was used as grease, but also for medical purposes to treat skin diseases. In 1858, a year prior to Colonel Drake, Professor Georg Konrad Hunäus initiated drilling in the Wietze region with the expectation of uncovering lignite deposits. Unfortunately, he “only” hit oil, but this way, today the “Hunäus drilling” is regarded as the first successful drilling for oil worldwide. The Wietze oil fields were active until 1963.
Figure 6. Oil well in Titusville, PA, USA.
In the beginning, the commercial use of oil was as a replacement for whale oil for lighting purposes. (One might even claim that without the discovery of oil, whales would have been completely eradicated.) However, soon after this, electric lighting was invented, and the just-established oil industry would have been history, were it not for the fact that cars with internal combustion engines were invented. Their huge fuel demand saved the business. The chemical industry rapidly switched to oil as the dominating raw material after World War II.
3 Criteria for Raw Materials Selection
In principle, the “Chemis-tree” can be grown based upon coal, gas, oil, or renewables. As shown in Figure 7, conversion pathways are available for all options.
Figure 7. Conversion pathways from raw materials to intermediates [4].
If cost alone would decide, coal and natural gas would by far be preferred over oil. This becomes even more visible if the raw materials are compared based on a “cost per ton of carbon” base rather than the usually applied market prices. Table 1 illustrates this impact. It also demonstrates that CO2 does not come without cost, as it holds value for applications like tertiary oil recovery. Tertiary oil recovery, or enhanced oil recovery, involves employing various techniques such as fluid injection or chemical processes to extract additional oil from reservoirs after primary and secondary recovery methods have been exhausted.
Table 1 further emphasizes the strong connection between chemistry and the energy sector by demonstrating that the cost of carbon is closely tied to the price of energy.
Table 1. Cost comparison for various carbon sources in $/ton and $/GJ.
Carbon source | $/tonC | $/GJ | Reference |
---|---|---|---|
-CH2– (oil) | 730 (365) | 21 (10.5) | @100(50) $/bbl (US dollars per barrel of oil) |
CH4 (gas) | 135 | 3.8 | @ 4$/MMBTU (USA) (price of natural gas in the United States) |
-CH- (coal) | 98 | 3.1 | @ 90$/ton (NWE) (price per ton in the specified market region, here Northwest Europe) |
saccharose | 1000 (630) | 26 (16) | @19(12)ct/lb (price per pound (lb) in cents) |
CO2 | 180 | — | @50$/ton (price per metric ton in US dollars) |
The conversion pathways from raw materials to the most important intermediate molecules, lower olefins and aromatics, differ significantly between oil and gas or coal, respectively. Whereas oil already has the required C:H ratio of olefins (CH2), this is not the case for natural gas (CH4) and coal (CH). The former includes too much, the latter too little hydrogen.
Figure 8. Schematic pathways from CH4 and “CH” (coal) to “CH2” (olefins).
Thus, in both cases, a “detour” via methanol is required (see Fig. 8). In the case of natural gas, excess hydrogen is removed as water, in the case of coal, the additional hydrogen is generated by means of the water gas shift reaction, which releases excess carbon as CO2.
The “detour” increases the investment costs for the respective plants, and, therefore, natural gas and coal only become economically superior if their cost is very much below the oil price—which currently is the case in the US for gas and in China for coal. In addition to fixed and variable costs, the decision to invest in a chemical plant, which is a very long-term economic asset, is influenced by factors such as raw material availability and existing or anticipated regulatory conditions. Among others, this includes considerations related to wastewater management and carbon emissions.
4 Sustainability
Counting in the process energy required (heat and electricity), about 20 % of the annual global industrial CO2 emissions originate from five basic industries (see Fig. 9). After the steel and cement industries, the chemical industry ranks third in this group—albeit on a lower level—followed by aluminum and paper production [11]. It is, therefore, also urgent for the chemical industry to reduce its CO2 emissions
Figure 9. Global industrial CO2 emissions [%] in 2018 [11].
In particular, the processes at the start of the production network are very energy-intense: steam cracking, syngas (hydrogen) production, and acetylene production. Typically, here the high-temperature process energy is provided by gas firing with associated CO2 emissions. A straightforward approach to reducing CO2 emissions is to initially replace gas firing with electric heating, assuming there is a reliable supply of electricity from renewable sources in adequate quantities. Currently, multiple companies are undertaking projects to test new technologies in pilot plants with multi-megawatt capacities [13].
Even more demanding is the reduction of CO2 emissions which are stoichiometrically linked to the synthesis of molecules. The most prominent example for this case is the synthesis of ammonia via the Haber–Bosch process, more precisely the supply of hydrogen to this process. Estimates are that this process alone contributes more than 1 % to the annual total global CO2 emissions. Consequently, there is a high need for hydrogen without associated atmospheric CO2 emissions.
Figure 10. Routes to hydrogen [4].
Figure 10 shows the technology options for hydrogen production, sometimes called “The Hydrogen Color Theory”. The current state-of-the-art method for producing hydrogen is through “grey” hydrogen, which involves steam methane reforming followed by water gas shift. However, this process leads to considerable energetic and stoichiometric CO2 emissions. If these emissions are captured and stored in underground reservoirs, the color of the resulting hydrogen turns into “blue”.
Water electrolysis driven by renewable electricity often is regarded as the royal road to climate-neutral “green” hydrogen. One has to consider, however, that due to the strong hydrogen–oxygen bond, very large amounts of electricity are required for the electrochemical splitting of this bond. If the electricity source would be nuclear, the hydrogen color changes to “purple/pink” or “yellow”.
Another, albeit less well-known, method of hydrogen production is methane pyrolysis, which offers the advantage of relatively low energy input. Instead of emitting carbon as CO2 into the atmosphere, solid carbon is obtained and has to be stored (“buried”) underground. Limited amounts of this by-product might also be sold as a product.
5 Future Carbon Sources
In a sustainable economy, fossil carbon sources should be replaced, or their use at least minimized. Photosynthesis in nature uses atmospheric CO2 as a carbon source and water as a hydrogen source to build carbohydrate and fatty acid molecules. Both contain significant molar fractions of hydrogen. The availability of large amounts of hydrogen without an atmospheric CO2 footprint, therefore, is the precondition for a CO2-based chemistry.
Moreover, it must not be overlooked that in the long run, CO2 needs to be captured from the atmosphere if a closed carbon loop shall be established, e.g., via direct air capture technologies. CO2 capturing technologies are under development, but a fundamental problem will remain: The low concentration of atmospheric CO2 will lead to costs way above the current CO2 market price of 50 $/ton CO2 shown in Table 1.
Figure 11. Renewable raw materials in the German chemical industry in 2016 (1000 tons/a) [14].
Instead of starting from CO2, carbohydrates and fatty acids that have already been synthesized by Nature are a second option to replace fossil carbon sources. Already, some 10–15 % of the raw material base are renewable. As shown in Figure 11 for the German chemical industry, oils and fats take the largest share, followed by carbohydrates, both edible and non-edible. Usually, these molecules are used in products where the natural building block is preserved to a large extent.
Significantly larger quantities of renewable molecules are used in the energy sector, with a particular focus on bio-ethanol as a potential alternative or additive to gasoline fuel. The green bars in Figure 12 show the 2021 production volumes of bio-ethanol in various regions of the world. For comparison, the respective gasoline consumption figures are also shown. In 2021, a total of nearly 75 million tons of ethanol were produced, which pales in comparison to the consumption of over 400 million tons of gasoline in the US and the EU27 countries alone.
Figure 12. Global bio-ethanol production in 2021.
Currently, the chemical applications of ethanol remain relatively limited. However, there are promising possibilities, as illustrated in Figure 13.
Figure 13. Chemistry options for the use of ethanol in competition with fuel use.
However, a crucial limiting factor to consider for the use of bio-molecules, whether for energy or chemical purposes, is the availability of arable land on our planet. This resource is also needed for food, and untouched land is essential for the functioning of the global climate system. In Brazil alone, more than 845.000 km2 of native vegetation were cleared from 1985 to 2021, mostly for agriculture [15]. This is nearly 2.5 times the area of Germany.
Figure 14. Brazil‘s shrinking forests [15].
6 Summary
For the time being, oil has become the dominant raw material for the petrochemical industry. This is due to the fact that oil offers direct access to olefins and aromatics, which serve as crucial starting points for the industry’s value-added chains.
Natural gas is an important energy carrier for the required process energy, and heavier components in natural gas are increasingly used as cracker feed instead of oil. Coal has a special role in China. On the one hand, it is a very inexpensive carbon source, on the other hand, it requires large investments due to solids handling, and last but not least its use is associated with high stoichiometric CO2 emissions.
Fatty acids and carbohydrates have found their place as renewable building blocks in selected compounds. Bioethanol might become an interesting addition in the future. However, for ecological reasons, renewables should not become the sole carbon source of the industry.
Like other industries, the petrochemical industry also needs to be transformed into a sustainable system and steered away from fossil carbon. This will, however, only be possible when large volumes of renewable electricity are available. In a first step, renewable electricity can replace fossil energy carriers for process energy. In a second step, hydrogen with no atmospheric CO2 footprint is required, and, in the future, atmospheric CO2 may become the source of carbon. Despite these changes, the petrochemical industry will continue to be based on carbon.
References
[1] The Future of Petrochemicals, Towards a more sustainable chemical industry, International Energy Agency (IEA), Paris, France, 2018.
[2] Energy Flow Chart for the Federal Republic of Germany in 2021, Arbeitsgemeinschaft Energiebilanzen, Berlin, Germany, 09/2022. (accessed May 16, 2023)
[3] VCI Energiestatistik, Verband der Chemischen Industrie (VCI), Frankfurt, Germany, 12/2022.
[4] BASF SE, Ludwigshafen, Germany
[5] Verbund—A characteristic of BASF, The Times, Nov. 1998.
[6] Jens Truog, 11 Fakten über Holzkohle, ofen.de 16. Juli 2015. [accessed May 16, 2023)
[7] Heribert Offermanns, Peter Schalke, Frank Retzlaff, Bevor das Erdöl kam, Nachr. Chem. 2020. https://doi.org/10.1002/nadc.20204092808
[8] Georg Kolling, Products of coal (coke, tar, gas) and their analysis, Pure and Applied Chemistry 1977. https://doi.org/10.1351/pac197749101475
[9] BASF Corporate History, Ludwigshafen, Germany.
[10] A. Mittasch, M. Pier, K. Winkler, BASF AG, Ausführung Organischer Katalysen, German Patent 415,686, 1925.
[11] Stefan Lechtenböhmer, Frank Peter, Vortrag: Technologie- und Politikoptionen für eine klimaneutrale Grundstoffindustrie; Handlungsoptionen für die Stahl-, Zement- und Chemieindustrie, Agora Energiewende, Berlin, Germany, 2019.
[12] Fabian Joas, Wido Witecka, Thorsten Lenck, Frank Peter, Fiona Seiler, Sascha Samadi, Clemens Schneider, Georg Holtz, Georg Kobiela, Stefan Lechtenböhmer, Katja Dinges, Karoline Steinbacher, Jonas Schröder, Thobias Sach, Matthias Schimmel, Christine Kliem, Martin Altrock, Wieland Lehnert, Jasper Finke, Yasin Yilmaz, Klimaneutrale Industrie, Schlüsseltechnologien und Politikoptionen für Stahl, Chemie und Zement, Agora Energiewende, Berlin, Germany, 2020.
[13] BASF, SABIC and Linde start construction of the world’s first demonstration plant for large-scale electrically heated steam cracker furnaces, BASF press release, September 1, 2022. (accessed May 16, 2023)
[14] Chances and limitations for the use of renewable raw materials in the chemical industry, VCI Position Paper, Frankfurt, Germany, 2015.
[15] MapBiomas Project, Collection 7 of the Annual Series of Land Use and Land Cover Maps of Brazil, August 2022. (accessed May 30, 2023)
Also of Interest
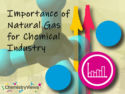
Hardly any other industry needs as much gas as the chemical industry; this Clever Picture explains why
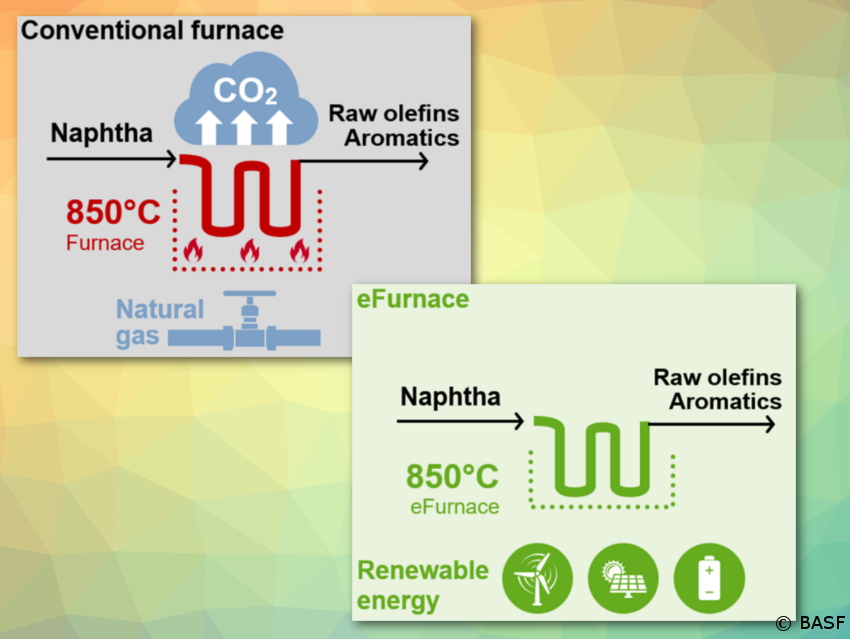
BASF, SABIC, and Linde join forces to demonstrate innovative concept to reduce CO2 emissions
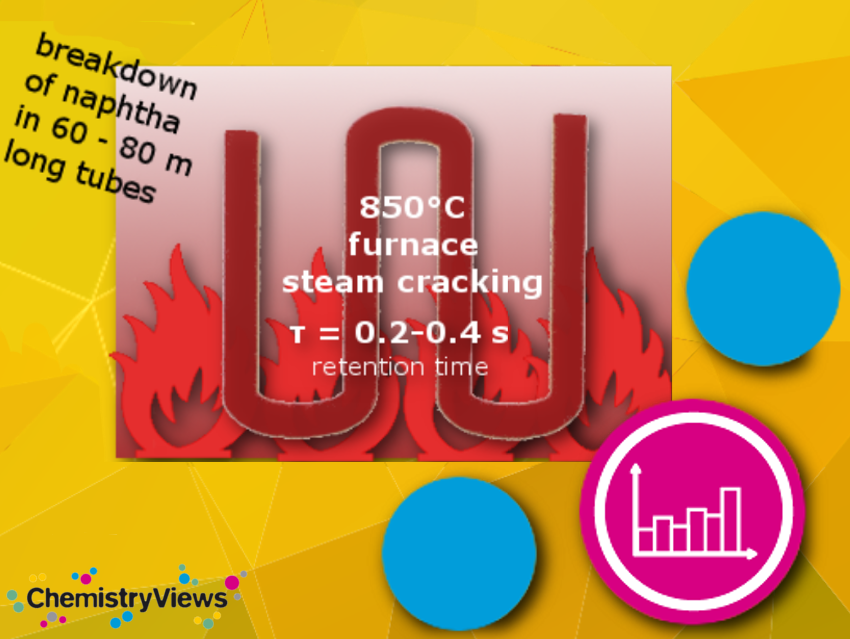
Learn from this picture how a steamcracker works